Introduction: "Ultimate Guide to Marine Epoxy: Everything You Need to Know"
The “Ultimate Guide to Marine Epoxy: Everything You Need to Know” is here! This extensive reference covers marine epoxy’s uses, benefits, and more. This article will help you navigate marine epoxy whether you’ve worked on boats before or not. Let’s begin!
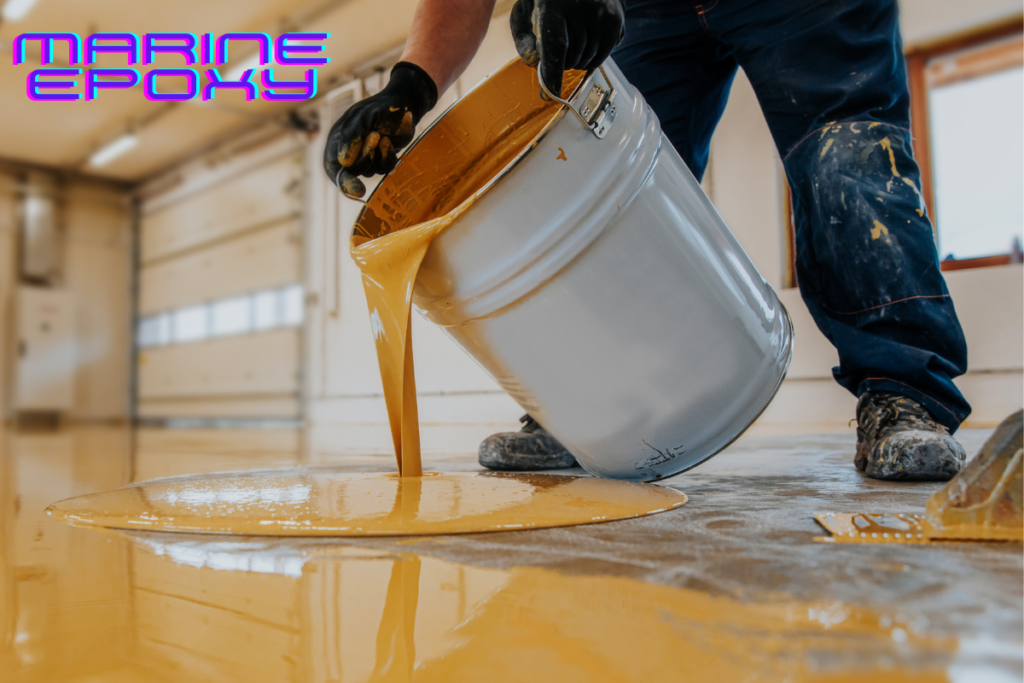
Meaning of "Marine Epoxy":
Marine epoxy adhesive or coating is designed for salt water. It is known for its strength, durability, and resistance to water, chemicals, and UV light. Marine epoxy is used to build, repair, and maintain boats and seal, bond, and protect water-contact surfaces.
Marine enthusiasts and pros like it because it can tolerate tough circumstances.
Why is "Marine Epoxy" so important for the Marine Environment?
Maritime epoxy is vital to the maritime environment due to its particular properties.
Saltwater epoxy benefits wildlife for these reasons:
Water Resistance
Marine epoxy resists water, making it ideal for sealing boat hulls, decks, and fittings. Water resistance makes marine buildings less prone to decay, rust, and be harmed by water.
Durability
Marine epoxy is durable and can withstand saltwater, UV radiation, and changing temperatures. Its strength keeps marine tools and structures safe and functional.
Bonding Strength
Marine epoxy bonds well to metal, plastic, fiberglass, and wood, which are commonly used in marine applications. This bonding strength ensures sturdy and dependable marine constructions and fixes.
Chemical Resistance
Marine epoxy can withstand several marine chemicals, oils, and fuels. Protecting maritime surfaces from chemical degradation and corrosion ensures their durability.
Marine epoxy helps the marine environment remain longer and be more sustainable by protecting marine structures, boats, and gear.
What about the application of "Marine Epoxy", is there any constraints related to "Marine Epoxy" application?
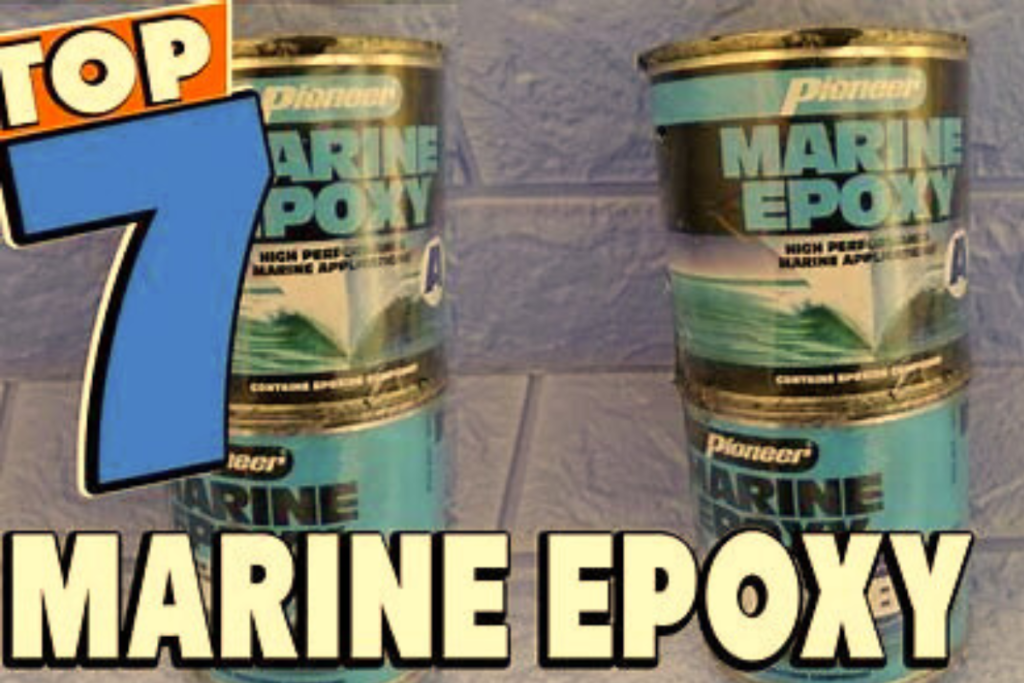
Strong and flexible marine epoxy is utilized in marine situations. There are several things to know about using it properly.
Please note these restrictions:
Surface Preparation
In order for marine epoxy to stick successfully, the surface must be adequately prepped. Surfaces must be clean, dry, and free of oil, grease, and previous paint to adhere well.
Temperature and Humidity
Temperature and humidity determine how quickly marine epoxy hardens. Following the manufacturer’s specifications is crucial because extreme temperatures and humidity can affect epoxy performance and cure time.
Mixing Ratio
Most marine epoxies cure well when the glue and hardener are combined properly. If you don’t follow the mixing ratio, the epoxy may not cure completely, weakening its bond and qualities.
Pot Life
Marine epoxy hardens after a specified time. This is “pot life.” Stick to it to make sure the tool works.
Ventilation
Proper ventilation is essential when working with marine epoxy to avoid inhaling dangerous vapors. If working in a compact space, wear respiratory protection or operate in a well-ventilated environment.
Compatibility
Marine epoxies are not compatible with all materials. The base and coating must be compatible to avoid adhesion or chemical reactions that could impair the application.
These limits and best practices for applying marine epoxy will ensure good results and maximize the epoxy’s effectiveness and durability in marine situations.
Why is "Surface Preparation" crucial for "Marine Epoxy"? How does it effect performance?
Preparing the surface before applying marine epoxy affects how effectively the coating or bond sticks, lasts, and works.
This is why surface preparation is crucial:
Adhesion
Making sure the surface is ready helps marine epoxy cling to the base. Dirty, unclean, or uneven surfaces might hinder epoxy bonding. This can induce bonding failure and coating removal.
Durability
A clean, solid surface provides marine epoxy a long life. Proper surface preparation removes defects and pollutants that could weaken the epoxy’s adhesion and cause it to break early
Uniformity
Preparing the region flattens the surface, making marine epoxy application and curing easier. Rough surfaces might change covering thickness, lowering performance.
Corrosion Protection
In marine situations with saltwater and corrosion, the epoxy coating must attach to a well prepared surface. A well-prepared surface prevents rust and extends foundation life
Impact Resistance
Marine epoxy is more impact-resistant on properly prepared surfaces. This implies it can withstand higher mechanical stress and wear. This is crucial in marine environments where rough weather can destroy surfaces.
Marine epoxy generates a durable bond or covering, thus surface preparation is crucial. Preparing the surface improves marine epoxy adhesion, lifespan, and performance.
How are temperature and Humidity going to affect the "Marine Epoxy" application and how its influence its performance?
Temperature and humidity affect marine epoxy use and performance.
They can alter marine epoxy application and performance:
Curing Time
Temperature and humidity determine marine epoxy cure time. Higher temperatures usually accelerate healing and lower temps slow it. Similar to humidity, drying times can be extended. To ensure epoxy cures properly and operates well, follow the manufacturer’s temperature and humidity recommendations.
Viscosity
Marine epoxy viscosity changes with temperature. Higher temperatures reduce viscosity. This simplifies epoxy spreading and application. The epoxy may be difficult to work with in colder temperatures because to increased thickness. Changing the temperature can assist balance an application.
Pot Life
Pot life is the period epoxy can be utilized after mixing glue and hardener. Lower temperatures prolong pot life, but higher temps shorten it. Temperature during application is crucial to maintaining pot life and avoiding quick curing or incomplete bonding.
Curing Quality
Epoxy drying quality is affected by temperature and humidity. Too high or low temperatures might cause incorrect curing, adhesion, or mechanical feature loss. Maintaining the environment during and after application helps form a strong relationship.
Long-Term Performance
Weather and humidity at application might affect marine epoxy performance. If the climate is wrong, the epoxy coating or bond may defect, last less, or breakdown early. Marine epoxy performs better and lasts longer when temperature and humidity are controlled.
In conclusion, monitoring and maintaining temperature and humidity while applying marine epoxy is crucial for optimal results and longevity in aquatic conditions.
Why is "Mixing Ratio" required for "Marine Epoxy"? How does it effect performance?
The mixing ratio shows you how much epoxy glue and hardener to combine for marine epoxy. The manufacturer provides the mixing ratio, which is crucial for utilizing marine epoxy properly.
Why the mixing ratio matters and how it affects performance:
Curing Process
The mixing ratio affects the chemical reaction that starts marine epoxy curing. Each type of epoxy cures best with the correct resin-hardener ratio. Without the recommended mixing ratio, the epoxy bond may not cure, have soft areas, or be weaker.
Adhesion and Strength
Proper glue and hardener proportions make epoxy stick and bond strongly. The coating or bond works better and lasts longer when the pieces are correctly combined because the epoxy clings to the base strongly.
Consistency and Workability
The mixing amount determines how sticky and workable marine epoxy is. Proper epoxy mixing produces a smooth, well-blended product that is easy to use, spread, and apply. Uneven curing, air bubbles, and poor adherence can result from mixing quantities.
Chemical Stability
Proper mixing ratios ensure chemically stable epoxy. A proper ratio ensures a robust hardener-resin connection. Epoxy’s chemical properties can be destroyed if mixed improperly, affecting its performance and durability.
Performance and Durability
Marine epoxy performance and longevity depend on mixing amount. The suggested mixing ratio ensures that epoxy dries properly, providing the best strength, adhesion, and protection from water, chemicals, and UV light. In marine applications, precise and accurate mixing ratios help epoxy last and perform well.
In conclusion, marine epoxy must be mixed properly to work, stick, and last. The epoxy will last and operate effectively in marine situations if you follow the manufacturer’s mixing ratio guidelines.
Describe "Port Life"? How does it affect the "Marine Epoxy" application and its performance?
An epoxy’s “pot life” is how long it can be utilized after the glue and hardener are mixed. When applying marine epoxy, pot life can greatly affect its performance.
Why pot life matters and how it affects marine epoxy use and performance:
Workability
The pot life indicates how long you can smooth, shape, and apply epoxy before it hardens. A longer pot life provides you more time and freedom to apply, smooth, and shape the epoxy coating or bond. To get a favorable result, finish the application on time.
Curing Control
Epoxy curing begins when its pot life expires. The epoxy dries and hardens after its pot life, forming a solid bond. Controlling pot life allows applicators to carefully time the application to ensure the epoxy sets evenly and effectively for optimal performance
Temperature Sensitivity
Room temperature and humidity affect pot life. Higher temperatures shorten pot life, while lower temperatures extend it. For best outcomes and pot life, applicators should consider the environment and labor length.
Quality Control
Quality control during application requires monitoring and managing marine epoxy’s pot life. Tracking pot life prevents premature curing, incomplete bonding, and inconsistent epoxy covering. Applicators can get the greatest results and keep epoxy strong by following the pot life.
Performance Consistency
Proper marine epoxy pot life management ensures consistent performance and results. Following the recommended pot life will ensure that the epoxy sets evenly, achieves the appropriate adhesion, strength, durability, and resistance. When pot life is handled properly, epoxy marine applications are sturdy and durable.
To conclude, marine epoxy pot life must be known and controlled for optimal performance, durability, and outcomes. Marine applicators may ensure epoxy cures, sticks, and protects by following pot life recommendations and considering weather considerations.
Why is ventilation needed for "Marine Epoxy"? How does it effect performance?
Ventilation is crucial when using marine epoxy. Proper airflow affects glue use and performance for numerous reasons.
This is why air impacts marine epoxy performance:
Safety
Ventilation provides safety when working with marine epoxy. Epoxy products can release toxic fumes and VOCs when mixing, applying, and curing. Good air spreads these toxins, reducing respiratory discomfort and health issues for applicators and nearby residents.
Air Quality
Good ventilation removes hazardous scents and toxins from the workplace, improving air quality. Adequate airflow prevents dangerous fumes from accumulating, making marine epoxy work safer and more enjoyable
Curing Process
Ventilation keeps air circulating and helps solvents evaporate, changing marine epoxy hardening. Good air flow removes water and solvents from the epoxy bond or coating, speeding cure. It helps smooth and level the finish when applied.
Application Consistency
Ventilation stabilizes marine epoxy application. Airflow prevents dust, grime, and other contaminants from clinging to epoxy, creating a clean, smooth finish. It also reduces defects that could affect epoxy performance or durability.
Product Performance
Poor ventilation can influence marine epoxy’s cure, stick, and overall performance. Without enough air movement, delayed sealing, uneven drying, and poor bonding might occur, causing the epoxy coating or bond to fail.
Applicators may make the work space safer and more controlled, increase air quality, speed up drying, and help marine epoxy perform better and last longer by ensuring enough air movement. Proper ventilation is crucial for epoxy applications in marine environments.
What is "Compatibility" and what should you watch out for when applying "Marine Epoxy"? how does it boost performance?
Marine epoxy “compatibility” refers to how well it functions with other materials or substrates during application or use. Making sure marine glue works with different materials is crucial.
How to check compatibility, apply marine epoxy, and optimize performance:
Definition
Checking for chemical, physical, and mechanical compatibility between marine epoxy and bases, coatings, coats, or structures is necessary. Incompatibility can cause epoxy to stick, delaminate, change color, or perform poorly.
Precautions during Application
- Test compatibility by applying a small amount of epoxy to a test surface and observing for reactions.
- Follow the manufacturer’s substrate, primer, and coating recommendations for appropriate adherence and performance.
- Clean and prepare the substrate per manufacturer instructions to ensure epoxy adhesion.
- Different epoxy types should not be mixed unless they function together.
Enhancing Performance
- Ensure the marine epoxy is suitable with the substrates for good adhesion and bonding, improving performance and durability.
- Compatibility minimizes peeling, cracking, and other layer or bond damage by forming a strong and smooth bond.
- Using suitable materials reduces the possibility of chemical reactions, coloration, or structure damage when blended.
Making ensuring the epoxy system is compatible and following marine epoxy specifications can increase its performance and lifespan. Making sure the epoxy works with the materials and conditions it will be exposed to keeps the bond strong and long-lasting, providing the finest maritime protection and performance.
Are there legal difficulties with marine applications since "Marine Epoxy" comes into close touch with aquatic life? How does "Marine Epoxy" suit their needs?
To safeguard maritime ecosystems, marine epoxy, especially in areas where it may touch marine life, must satisfy legal and environmental guidelines.
The following legal difficulties arise with marine usage and maritime epoxy can address them:
Environmental Regulations
Ocean chemical and material use is regulated to safeguard marine life and the environment. Marine epoxy manufacturers must observe the Clean Water Act, Marine Protection, Research, and Sanctuaries Act, and other environmental requirements to protect marine habitats.
Biocompatibility
Marine epoxy formulations may need to meet biocompatibility criteria to protect marine life. To prove the epoxy is environmentally safe, it may be tested for toxicity, chemical release, and marine life impact.
VOC Emissions
VOCs are controlled because they harm the environment and air. Marine epoxy manufacturers make low-VOC or zero-VOC products to reduce emissions and comply with marine environment regulations.
Product Labeling and Compliance
Marine epoxy products must have labels with safety, disposal, and environmental information. Compliance with regulations and accurate labeling helps consumers use products safely and responsibly at sea.
Third-party Certifications
Some marine epoxy products are certified by Green Seal or EcoLogo to meet environmental criteria. These certifications confirm that the epoxy has been examined for environmental impact and meets strict standards.
Following environmental rules, showing biocompatibility, decreasing VOC emissions, providing correct product information, and gaining third-party certifications can help marine epoxy makers meet regulatory requirements and promote environmentally acceptable use. These laws protect marine ecosystems and ensure epoxy-using marine industries employ sustainable techniques.
Conclusion: "Ultimate Guide to Marine Epoxy: Everything You Need to Know"
Finally, our “Ultimate Guide to Marine Epoxy” has covered everything about this marine application material. We examined the most significant aspects of marine epoxy use, including its definition, uses, restrictions, and factors that affect its performance.
We’ve discussed how vital it is to prepare the surface, maintain temperature and humidity, apply the proper mixing ratios, monitor the pot’s life, ensure air movement, consider compatibility, and consider marine legal considerations. Marine epoxy can assist marine enterprises become more ecologically friendly if best practices, safety, and environmental requirements are followed.
Marine epoxy is needed for boat building, repair, maintenance, and other water-related applications. Because it’s sturdy, durable, and chemical-resistant, it’s perfect for safeguarding marine buildings and improving equipment.
Marine enthusiasts, boat owners, and marine industry workers must grasp the basic rules and best practices for applying marine epoxy to get the best results and be environmentally responsible. Use this guide’s advice to choose wisely and maximize marine epoxy in your projects.
Thank you for using the “Ultimate Guide to Marine Epoxy”. This thorough guide should have provided you the information and resources you need to make informed choices and utilize marine epoxy successfully in your projects. Marine epoxy can help your next water projects last, operate effectively, and be environmentally friendly.
Marine epoxy can last anywhere from 5 to 10 years, depending on how it is used and the conditions. It is a durable material that is good for marine settings.
Yes, marine epoxy is waterproof and very resistant to water. This makes it perfect for making boats, fixing boats, and keeping boats in good shape.
Pingback: Ultimate Guide to Marine Epoxy Resin: Best products in 2021